<<Return to COTEC NEWS Menu
塗膜過多は塗料のムダ使いであり、また膜厚の過不足に起因する不良は多種に及ぶ。直接的には、ダレ、スケ、色差異常となって現れる。さらに、ワキ、発泡、フクレ、剥離(はくり)等も原因調査の結果、膜厚の過不足によるものであることが少なくない。不良品の補修・対応にかかるコストは、通常品の数倍以上と言われており、ライン生産においては、塗料のムダ吹き以上に不良による損害が収益を大きく圧迫する。 |
塗料システムの効率性・収益性向上を目的とし、膜厚に起因する不良ゼロを目標に膜厚管理を考える時、目的に沿った機器・方法・システムを選択することが最も重要となる。本稿では、膜厚計のメカニズムより、むしろ膜厚計を選択するうえでのポイントや、使用上のヒントをエルコメーター社の膜厚計を例に取り上げて、考えてみたいと思う。 |
第1図 膜厚管理方法の選択(例)
|
1.第一歩は多くの選択肢を考える |
第1図は、膜厚管理を考える上うえでの主な選択肢をチャートにしたものである。
|
2.接触式か非接触式か |
ず、接触式か非接触式かを検討することになる。塗膜に接触することなく塗膜を測定する非接触方式には、光干渉方式や変位計などがある。自動化が容易で塗膜を損傷させることがないので理想的な方法であるが、まだ制約条件やコストの点で、一般塗装ラインで採用するにはハードルが高いようである。 ここで、非接触により粉体塗料の硬化前層の厚みを計るものがあるので紹介したい。 |
(2)超音波式の硬化前粉体用膜厚計 |
@特徴 |
高価ではあるが、接触させることなく硬化前のパウダー状態の層厚を測定できる。後述する接触式の粉体膜厚計と対照的な特徴を持っている。 接触とは言え、測定ごとに位置・角度の微調整が必要なことから、自動化は一般的に困難である。前述のインラインの非接触測定方法とは一線を画すものである。 |
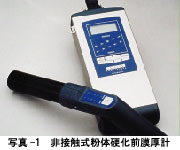 |
A膜厚計の例 |
実例を写真−1に示す。 |
B測定方法 |
|
a. |
塗膜に直角になるようにプローブ先端を接近させる。 |
b. |
距離調整用LEDインディケータが最適に示すように塗膜との距離を調整する。 |
c. |
角度調整用LEDインディケータが最適に示すように塗膜との角度を調整する。 |
d. |
距離と角度の両方が最適になると自動的に計測して、1〜2秒後に硬化後膜厚を推定して表示する。 |
|
3.接触式膜厚計 |
次にウエット塗膜で測定するか、乾燥後の塗膜で測定するかを検討したい。
ウエット塗膜とは乾燥前の塗膜(ぬれ塗膜)を言う。JISでは「ぬれ膜厚」、その膜厚計を「ウエットフィルム膜厚計」と表記している。
ウエット膜厚計は、乾燥前の塗膜に触れるため、測定跡を塗膜に残すことになるが、特徴を効果的に利用している現場も少なくない。 |
(1)ウエットフィルム膜厚計(ぬれ膜厚の評価) |
乾燥塗膜で測定するのが一般的であるが、条件の標準化ができない極端な多品種塗装や、乾燥まで時間を要する現場塗装では、ウエット膜厚計が効果的に利用されている。 |
@くし形ウエットフィルム膜厚計 |
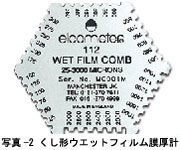 |
(1)特徴 一般に次に示すロータリー型に比べて精度は劣るものの、当てるだけで測定できるので、接触面積が最小で済む。 |
(2)膜厚計の例 実例を写真−2に示す。この例では、くし形測定部×6辺であるが、×2辺のモデルもある。 |
(3)操作手順 |
|
a. |
膜厚計を測定作業中にズレないように、そして素地に垂直に達するように塗膜中に当てる。 |
b. |
膜厚計を塗膜から外して、塗膜に触れている最も短い歯がどれか調べる。 |
c. |
最後に触れた歯と最初に触れなくなった歯の間にある数値を読み取る。 |
|
Aロータリー式ウエットフィルム膜厚計 |
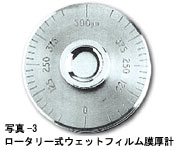 |
(1)特徴 膜厚計を塗膜上で回転させるために塗装接触面積は大きくなるが、この製品例では精度は±5%と比較的高い。 |
(2)膜厚計の例 実例を写真−3に示すと共に、その構造を第2図に示す。 |
(3)測定手順 |
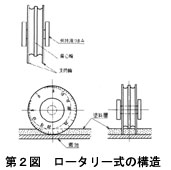 |
|
a. |
保持用のつまみを持って最大の数値を下に、支持輪(外輪)が素地に水平に達するように塗膜中に当てる。 |
b. |
素地上をころがるように塗膜中をほぼ360°ゆっくり回転させ、塗膜から外す。 |
c. |
偏心輪(中央輪)を見て、塗料が最初に付き始めた箇所、および付着した塗料の切れ目の数値を読み、二つの数値の平均値を測定値とする。 |
|
B粉体硬化前用くし形膜厚計 |
(1)特徴 ウエットフィルム膜厚計を粉体塗膜用に応用したものであるが、使い方は少し異なる。粉体塗装の場合、硬化前塗膜に接触させても、ブローして再塗装を行うことが比較的容易なので、製品化されたものである。 |
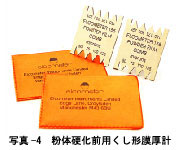 |
(2)膜厚計の例 実例を写真−4に示す。 |
(3)操作手順 |
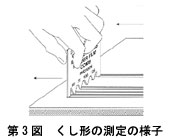 |
|
a. |
膜厚計を素地に垂直に達するように硬化前塗膜(粉体層)中に当てる。 |
b. |
第3図のように、素地に接しさせながら動かす。 |
c. |
膜厚計の歯が塗膜に残した跡を観察する。 |
d. |
最後に跡を残した歯と最初に塗膜に触れなくなった歯の間にある数値を読み取る。 |
|
4.乾燥後の塗膜の測定 |
非破壊式か破壊式かを検討することになるが、通常は非破壊式では測定できないあるいは実用的でない場合に破壊式を検討することになる。一般的な塗装・膜厚では、磁性金属素地上の非磁性塗膜には磁気方式による非破壊膜厚計が、非磁性金属素地上の非導電性塗膜の場合には、渦電流方式による非破壊膜厚計が利用されている。 |
(1)磁性体素地と非磁性体素地 |
第1表に、その代表例を示す。ステンレスには材質組成によって、磁性体も非磁性体もあるので注意したい。 |
第1表 磁性金属用膜厚計と非磁性金属用膜厚計で測定できるもの(例)
磁性金属用膜厚計で測定できるもの |
塗膜および皮膜 |
塗膜およびインキ、金属溶射膜(アルミや亜鉛などの非磁性金属)、ラバー、ほうろう、ガラス、亜鉛メッキ(亜鉛どぶづけ)や硬質クルムメッキなどのメッキ(電解ニッケルケッキは測定不可)、樹脂ライニング |
素地金属 |
鉄、鋳鉄(鉄鋳物)、マルテンサイト系ステンレス(磁性) |
非磁性金属用膜厚計で測定できるもの |
塗膜および皮膜 |
硬化した塗膜およびインキ、ラバー、ほうろう、ガラス、陽極酸化皮膜 |
素地金属 |
アルミ、銅、オーステナイト系ステンレス(非磁性) |
|
なお、両用タイプというモデルもある。これは、膜厚計が被塗物の素材を判断して、それぞれのモードを自動的に判断して測定する。磁性体製品と非磁性体製品が混在する塗装工場では有効である。
なお、弱い磁性を帯びた素材の場合には、両用タイプでは誤動作を起こすことがあるので、強制的に非磁性モードに固定して測定するとよいようである。 なお、磁性金属用膜厚計で鉄素地上の亜鉛メッキ層を測定することが可能であるが、重量法による値より少な目に表示されるので注意が必要である。鉄素地と亜鉛メッキ層との境界ははっきりしたものではなく、連続的な合金層となっている。膜厚計では、亜鉛メッキ層のうち磁性の強い合金層部分は素地としてみなしてしまうので、この分が少なく表示される。あらかじめ換算表を作成しておくとよい。 |
(2)精度についての注意点 |
一般に精度の表示としては、@「±2%+1μm」あるいはA「2%もしくは±2.5μmの大きいほう」といった表現が用いられている。これらの表現は、塗膜がかなり薄くなると精度的に不利になることを表している。磁気方式、渦電流方式ともに薄膜の測定には不向きであることがわかる。 後の項で述べるが、装置固有の精度以上に、校正(ゼロ調整)が正しく行われているかどうかが、実際の測定精度に大きく影響するので注意されたい。 |
(3)測定するうえでの注意点 |
膜厚計は、物差しのような絶対的な測定器ではない。相対測定法(計測工学では「置換法」)と言われるもので、校正(調整)という準備作業をして初めて測定が可能になる。膜厚計には製造工程で、メーカーの標準素地から得られた基準検量線(曲線)が記憶されている。
測定するうえでの注意点をまとめると以下のようになる。 |
|
(1) |
測定する対象製品の素地か、それと同等の特性を持ったもので校正を行う。 |
(2) |
フォイルは測定する膜厚に近く、なおかつ、少し厚めのもので校正を行うと精度が良くなる。 |
(3) |
フォイルは一般にプラスチック製であるので、使用していると傷むため定期的に交換する。 |
(4) |
製品が温度を持っているうちは誤差が生じるので、常温に冷えるまで待って測定する。 |
(5) |
1点で値を決めるのではなく、測定対象領域で、数点程度の測定を実施し平均値で示す。 |
(6) |
プローブ先端の磨耗等により精度に狂いが生じてくるので、定期的に精度チェックを行う。 |
|
(4)グレードを選ぶうえでのポイント |
パソコンでデータ処理を行うか、バッチ処理を行うか、などが選択のポイントとなる。バッチ処理は、特に多品種塗装においては有効な機能となる。 現場での電源確保が難しいため、プリンター内臓やポータブルプリンターを用いて、その場で印字することも検討されると思う。一般に、プリンター部の駆動は電池の消耗が大きいので、不意の電池切れに注意されたい。最近のPCとの連携ソフトは優れているので、膜厚計にデータを蓄えておいて、後でまとめてPCにデータを移して統計処理をしたり、PC用のプリンターで出力したりする使い方が一般化してきた。
|
5.プローブ体型化分離型か |
一体型(写真−5参照)では、片手での操作が可能になる。平板状の対象物を迅速に測定するのに優位性がある。また、安全性の点から、片方の手は自由にしておきたい高所での測定にも適している。 片手での素早い作業でも、プローブが正しく塗膜に接するように、各メーカーでは工夫を凝らしている。
エルコメーターでは、Big Footと呼ばれるガイド(写真−6参照)が、膜厚計の測定角度を規制し正確な測定をサポートしている。また、フィッシャー社製では、2点支持を採用して測定の安定性を確保しているが、これも工夫の好例である。 色ムラ等へのユーザーの目が厳しくなっていることから、膜厚管理への要求も変化している。従来は測定が困難であることから免除されていたような、コーナー部や凹部などの膜厚管理も項目に加えられるようになっている。このことから、用途に合わせて、最適な形状、特性の物を選択できる分離型の膜厚計(写真−7参照)と充実した交換用プローブラインアップの存在が重要な選択の要素となっており、複数種を用意しておくとよい。
|
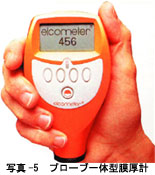 |
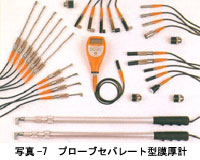 |
(1)さまざまなプローブの例 |
標準ラインアップ品の中で、微細な箇所の測定に適したいろいろなミニチュアプローブを写真−8に示す。 |
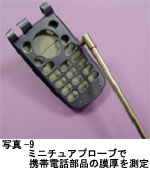 |
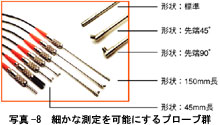 |
また、その使用例を写真−9に、ステンレスの磁性について第2表に示す。 |
|
|
第2表 ステンレスの磁性
磁性あり |
Cr系 |
マルテンサイト系(13Cr系) |
SUS4XX |
431,403,410,420,440など |
フェライト系(18Cr系) |
SUS4XX 4XX |
430,405など |
磁性なし |
Cr-Ni系 |
オーステナイト系(18-8系) |
SUS3XX,SUS2X |
304,304L,316,316Lなど |
|
6.使用上のヒント |
(1)精密機械としての膜厚計の取り扱い |
膜厚計は精密機械である。それなりの取り扱い上の注意を要するが、塗装現場ではなかなか理想的な取り扱いができない。操作部や表示部に塗装が付着して使えなくなった例も見受けられる。このような場合には、主要部にクッキング用のラップを巻いておくとよい。 |
(2)精度の劣化 |
プローブ先端は塗膜や素地と接するために磨耗を起こす。磨耗が進むと特性が異なり誤差が拡大する。膜厚計の不具合で最も多い要因ではないだろうか。
|
1. |
先端をたたくように塗膜に当てたり、押し当て圧を強くしすぎたりしない。 |
2. |
塗膜で先端をこすらない。 |
3. |
先端を常にきれいに保つ。 |
ことが大切である。 |
|
ザラザラした塗膜や硬いメッキ層の計測では、磨耗が大きくなりがちである。厚みがわかっている薄いフィルムをはさんで計測するのも一つの対応策である。
|
7.プラスチック塗装 |
素地が樹脂の場合には、一般に磁気方式や渦電流方式では測定できない。しかし樹脂素地の下に金属板を密着できる場合には、上述の膜厚計でも測定可能な場合がある。金属板の上の樹脂+塗膜を膜厚として測定する。塗膜後の膜厚から塗装前の膜厚を引いたものが、実際の塗装の厚みとなる。素地金属は一定以上の厚みがあることが必要で、膜厚計によりその条件は異なる。樹脂に当てる金属板の選択には注意していただきたい。 それ以外の場合には、塗膜を削って測定する破壊式があり、代表的なものとしてはくさび形切削法がある。非破壊方式では超音波式膜厚計が挙げられている(超音波式膜厚計については各メーカーの説明に譲るが、1度に3層までの各層の厚みを測定できるものもある)。 |
(1)くさび形切削法 |
|
@特徴 |
塗膜を削らなくてはならないが |
1. |
硬すぎて切削できない。 |
2. |
もろくて砕けてしまう。 |
3. |
軟らかすぎて形状を保てない。 |
|
ということがなければ、あらゆる塗膜に適用が可能である。 |
A膜厚計の例 |
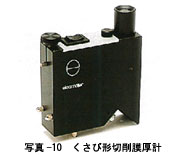
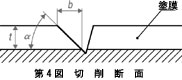 |
実例を写真−10に示す。 |
B測定手順 |
|
1. |
切削部の見分けを容易にするために、あらかじめ塗装色と対照的な色のフェルトペンで、切削する塗膜部に色を付ける。 |
2. |
工具にくさび状の刃を固定する。 |
3. |
工具のガイド足をしっかり塗膜に押し付けながら、工具を動かして素地に達する断面が、くさび形になるように塗膜を切り取る。 |
4. |
顕微鏡でくさび状の切込みを観察し、第4図のbの寸法を測定する(αの切削角度はJISにより膜厚ごとに規定がある)。 |
5. |
次式により膜厚(t:膜厚μm)を算出する。
t=b×tanα |
|
さらに選択肢を広げて考えてみる。膜厚を管理する手段は膜厚計ばかりではなく、マイクロメーターやノギス、さらには重量も膜厚を管理する方法として有効である場合もある。 塗料のムダは、膜厚の過多にもよるが、一般にスプレー条件や塗着率の影響が大きい。一般に、塗着率というとスプレーガンの特性に依存すると考えがちだが、現実には、被塗物の引っ掛け密度やジグの工夫による影響も大きい。さらには、レシプロからスプレー位置・角度の自由度の大きいロボットのほうが、トータル塗着率を考える時に有利になる。塗着率の向上策は、膜厚の均一性にも寄与することが多いので、総合的に対策を講じたい。 不良の解消をするための膜厚管理という目的主体で考える時、さらに膜厚管理の手段について柔軟に考える必要がある。製品に色ムラに対する市場のクレームに苦慮していた塗装工場でのことである。2層のトップコートの膜厚不足が、隠ぺい性の不足を招き色ムラとなって現れていた。当然、現場では1品ごとに膜厚を正確に測定し、その値に応じてその都度塗装条件を微調整する必要性を感じ、膜厚計導入について相談依頼を受けた。まず提案したのは、アンダーコートの色を淡くすることと、色ムラの限度見本づくりの検討であった。 膜厚管理に重要なことは |
|
1. |
必要以上に測定精度を上げてしまうことで、管理幅が狭くなり過ぎないようにする。 |
2. |
対策が膜厚管理に依存し過ぎるのを避ける。 |
3. |
量産ラインでは、全量測定検査といった測定頻度の過多を必要とするような塗装システムそのものの再検討。 |
が重要となる。 |
|
膜厚管理の目的は、塗膜厚を正確に記録することではなく、膜厚に起因するムダや不良をゼロにすることと考えるなら、膜厚管理を必要以上に厳しくすることは、むしろ目的に反する。膜厚計を利用するうえでの重要なポイントであると思う。 最近のナノコートレベルの膜厚要求が出てくると、レーザーの応用など膜厚測定技術もまた違った顔ぶれが増えていくと予想される。膜厚管理は今後ますます重要性を増すであろう。
|
<<Return to COTEC NEWS Menu | TOP |
 |
Copyright(C) 2004-2025 COTEC Co.,Ltd. All rights reserved. 無断転載、転用はご遠慮ください |