粘度の定義
高粘度用試験に用いたのは27,000mPa・s※の接着剤です。
高粘度、中粘度、低粘度の定義は業界によって違うようです。
バーコーターが扱う塗工液は塗装業界~接着業界までを包含するので、100mPa・sまでを低粘度、100以上~10,000mPa・sを中粘度、10,000mPa・s以上を高粘度と便宜上定義しました。
ちなみにオリーブオイルが100mPa・s程度、トマトケチャップが1,000mPa・s程度、はちみつが10,000 mPa・s程度です。
※:mPa・s:ミリパスカル秒。1mPa・s=1cp
開発したワイヤレスバーコーターの形状
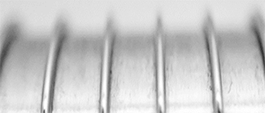
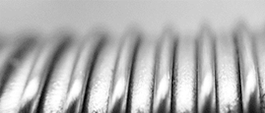
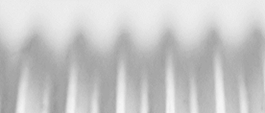
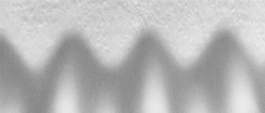
これまでバーコーターと言えば Fig1 のようにステンレスの細いワイヤを強固にバーに巻き付けたスパイラルワイヤバーコーターでした。
JIS K5400 3.3 試験片の作成、 7.塗り方 の 7.5.バーコーター の項でバーコーターの規格は以下のように説明されています。「針金(ワイヤ)の直径によって番号がついている。番号は針金の直径をミル単位※で示しており、番号が大きい方を用いると厚く塗ることができる。」
一般に番号ごとにそのバーコーターで塗ることができるウェット膜厚が示されていますが、これはあくまで目安で、実際にメーカーにより同じ番手でもウェット膜厚の表記が異なることがあります。JIS K5600-4-1 に「同じフィルムアプリケーターを用いても操作者が異なる場合には著しく異なった膜厚の塗膜が得られるので絶対的な方法が要求される」と記されているように、塗工液の粘度、バーコーターの走行(移動)速度などにより実際のウェット膜厚は大きく異なります。
塗膜は、Fig2 のようにワイヤとワイヤの間に入った塗工液により形成され、ワイヤ径が大きいほどその断面積は大きくなるので膜厚が大きくなります。
※ミル(mil):主に米国で採用しているヤード・ポンド法による長さの単位。1ミル=1000分の1インチで約0.0254mm(25.4μm)。例えば、No.2のバーコーターの線径は 2 mils となっています。
しかし、厚膜なると線径を太くするだけでは追いつかなくなり、また巻ける線径にも限界があるため、間隔をあけて巻くことになります。これを Gapped Wound (ギャップ巻)と呼びます。しかし、間隔をあけると使用してうちにワイヤがずれてしばしば偏りを起こします。そこで、2重に巻いてワイヤのズレを防ぐという方法が取られる場合があります。これは Double Wound (ダブル巻)と言われる手法ですが、コストがかかりまたワイヤ間の隙間が複雑になり逆に清掃が難しくなります。ギャップ巻とダブル巻にはそれぞれ避けがたい短所があります。
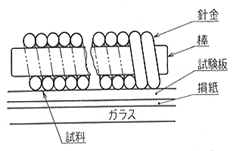
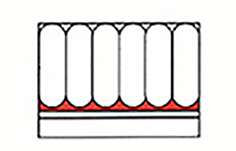
実験結果1.ウェット膜厚理論値と乾燥膜厚の関係
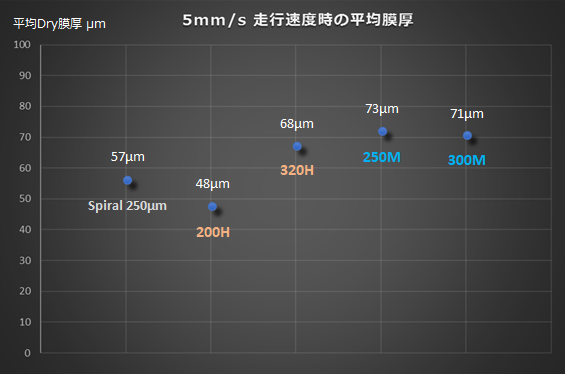
27,000mPa・sの高粘度の接着剤を塗工液として用いました。
Spiral (スパイラルワイヤバーコーター) の場合
Spiral (スパイラルワイヤバーコーター)として使用したのは、メーカー公称250μm用の#110のギャップ巻タイプです。250μmというのは、凹部の断面積に100%塗工液が保持され塗工されたという前提で計算された理論値です。高粘度ほど凹部に塗工液は入りきらずに移動していくため、実際のウェット膜厚とは一般に大きくかけ離れた値になります。このケースでは理論値の対して乾燥後の膜厚は1/4以下となっています。
ワイヤレスバーコーター Mタイプ の場合
理論値では250μm用と300μm用を用意しましたが、両方とも70~75μmの間になりました。この結果から、中粘度を中心に設計されたMタイプで、かなりの高粘度である27,000mPa・sの塗工液を塗工するのは難しいことがわわかります。凹部に塗工液が入らないうちにバーが移動してしまっていることを示しています。
ワイヤレスバーコーター Hタイプ の場合
良好な結果を示しています。理論的な膜厚値を変化させると、それに伴って乾燥塗膜も増減しています。続いてバラツキについて検証してみたいと思います。
実験結果2.膜厚のバラツキ
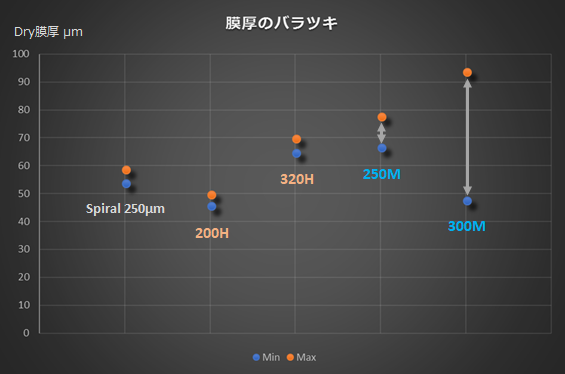
1回の塗工で形成された塗膜の膜厚を9か所測定して、その最大値と最小値をグラフ化しました。
塗工速度は5mm/秒です。
ワイヤレスバーコーター Mタイプ はバーの凹凸パターンがそのまま塗膜に模様(ワイヤレスバーコーターで言うところのワイヤ痕)として残ってしまい、塗膜の凹凸がそのまま膜厚のバラツキとなって表れています。
続いて操作のしやすさ(走行速度の管理幅のゆとり)についてみてみましょう。
実験結果3.速度の変化が平均膜厚に及ぼす影響
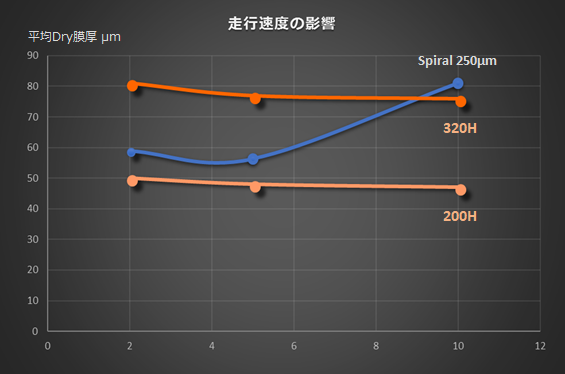
ワイヤレスバーコーター Mタイプ は除外し、Spiral (スパイラルワイヤバーコーター) と ワイヤレスバーコーター Hタイプ を使用して、走行速度と膜厚の関係を検証してみました。
Spiral (スパイラルワイヤバーコーター) の場合
とても不規則に膜厚が変化しています。JIS K5600-4-1の序文に、「同じフィルムアプリケーターを用いても操作者が異なる場合には著しく異なった膜厚の塗膜が得られるので絶対的な方法が要求される」と記されていますが、そのように記された理由をここからもうかがい知ることができます。
ワイヤレスバーコーター Hタイプ の場合
速度が変化しても膜厚はかなり安定しています。塗工液が凹部に入る→移動にともなって凹部の塗工液が基材に供給される→供給されながら3次元的にレベリングする・・・のサイクルが円滑に行われやすいことを示しています。
続いて、バーコータで高粘度の塗工液を塗工した際の最大の難敵・・・ワイヤ痕の発生状態についてみてみたいと思います。
実験結果4.外観(スジ状のワイヤ跡)の確認
2mm/s時 | 5mm/s時 | 10mm/s時 | |
---|---|---|---|
Spiral 250μm | ![]() |
![]() |
![]() |
200H | ![]() |
![]() |
![]() |
320H | ![]() |
![]() |
![]() |
グリーンライトは凹凸を際立たせて見せる効果があります。
走行方向に対して横方向から光を当てて、走行方向に沿って生じるワイヤ痕の有無を確認しました。画像中の矢印が走行方向です。
Spiral (スパイラルワイヤバーコーター) の場合
理想的な走行速度は2mm/秒もしくはそれ以下です。2mm/秒でもわずかにワイヤ痕が確認されます。2mm/秒より速くなると、塗工液が凹部に入る→移動にともなって凹部の塗工液が基材に供給される→供給されながら3次元的にレベリングする・・・というサイクルは減少し、熊手で塗工液をひっかいて延ばしているような状態になっていきます。そのため膜厚の制御もできなくなります。
2mm/秒~10mm/秒の走行速度の変化を避けることは、手でバーコーターを持って塗工する場合には不可能です。手でバーコーターを操作することをJIS/ISOが警告しているのはこのためです。
ワイヤレスバーコーター Hタイプ の場合
Spiral (スパイラルワイヤバーコーター)に比較して格段に安定した外観を示しています。
200μm用と320μm用とを比較すると、320μmの方がワイヤ痕状の模様が残りやすいようです。厚膜にするほど、速度の管理幅はより狭くなるようです。